Seasonal Dust Control: Adapting Strategies Throughout the Year
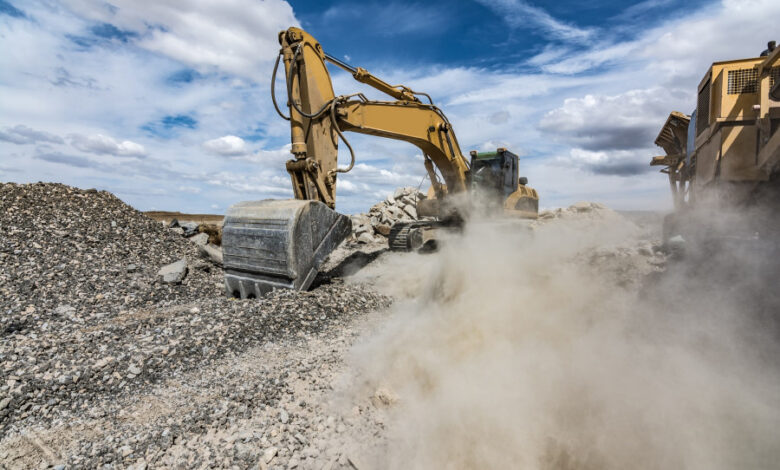
Dust control is a challenge that fluctuates significantly with changing seasons. Weather conditions such as temperature, humidity, and wind patterns play a major role in determining how effective BossTek dust suppression methods will be. Therefore, it’s essential to adapt strategies that align with seasonal conditions and maintain efficiency, compliance, and safety. Additionally, a proactive approach to seasonal dust control ensures businesses can address dust challenges effectively, regardless of the time of year.
Managing dust in winter
Winter brings unique challenges for dust suppression, as freezing temperatures and snow can limit the effectiveness of traditional water-based methods. Ice formation from water applications can create safety hazards and disrupt operations. Instead, businesses often rely on chemical suppressants designed to perform well in cold conditions. These suppressants form a protective layer that prevents dust particles from becoming airborne without requiring excessive water. Additionally, managing traffic patterns on unpaved roads and ensuring proper drainage can help minimize dust issues during the winter months.
Dust control during the dry spring season
Spring often marks the transition to drier weather, with increased winds and reduced ground moisture. These conditions can worsen dust problems, particularly in industries like construction and agriculture. During this season, water-based methods such as sprinklers and water trucks regain effectiveness but may need to be used more frequently. Misting systems can provide targeted suppression in high-traffic areas, while chemical solutions may offer long-lasting results for larger spaces. Regular monitoring of dust levels is essential to adjust strategies as weather conditions fluctuate during the spring.
Addressing summer dust challenges
Summer is typically the most demanding season for dust control, with high temperatures and low humidity creating ideal conditions for dust to become airborne. Water evaporation rates are higher during summer, reducing the effectiveness of water-based suppression methods. Chemical suppressants that bind dust particles are a practical alternative, as they require less frequent application and remain effective even in extreme heat. In areas with heavy equipment or vehicle traffic, dust collection systems and localized misting can also play a critical role in keeping dust levels under control.
Controlling dust in the wet fall season
Fall often brings increased rainfall, which can temporarily reduce dust levels but also create new challenges. Mud and wet dust can become problematic, especially in industries like mining and construction, where equipment and vehicles can spread debris across sites. Proper drainage systems and surface maintenance are essential to prevent waterlogged areas from turning into sources of fine dust when dry weather returns. During this season, dust suppression efforts may focus on maintaining clean and stable work surfaces rather than active suppression.
Monitoring and adapting strategies year-round
The key to successful seasonal dust control is ongoing monitoring and flexibility in adjusting strategies. Advanced dust monitoring systems can provide real-time data on airborne particles, helping operators identify trends and adapt methods to current conditions. Incorporating predictive analytics can further enhance efficiency, allowing businesses to prepare for seasonal changes before they occur. Regular training of staff ensures that teams are equipped to implement the most effective dust control measures for each season, minimizing disruptions and maximizing operational efficiency.
Seasonal dust control requires more than a one-size-fits-all approach. By adapting strategies to align with the unique challenges of each season, businesses can ensure effective suppression throughout the year. A dynamic approach to dust control not only addresses seasonal challenges but also positions businesses for long-term success in managing this critical operational concern.